ダイ/モールド製造や車両識別番号では、レーザー刻印をミリメートルレベルの深さまで施す必要があります。必要な深さに到達するには、多くの場合、層毎に複数回加工する必要があります。
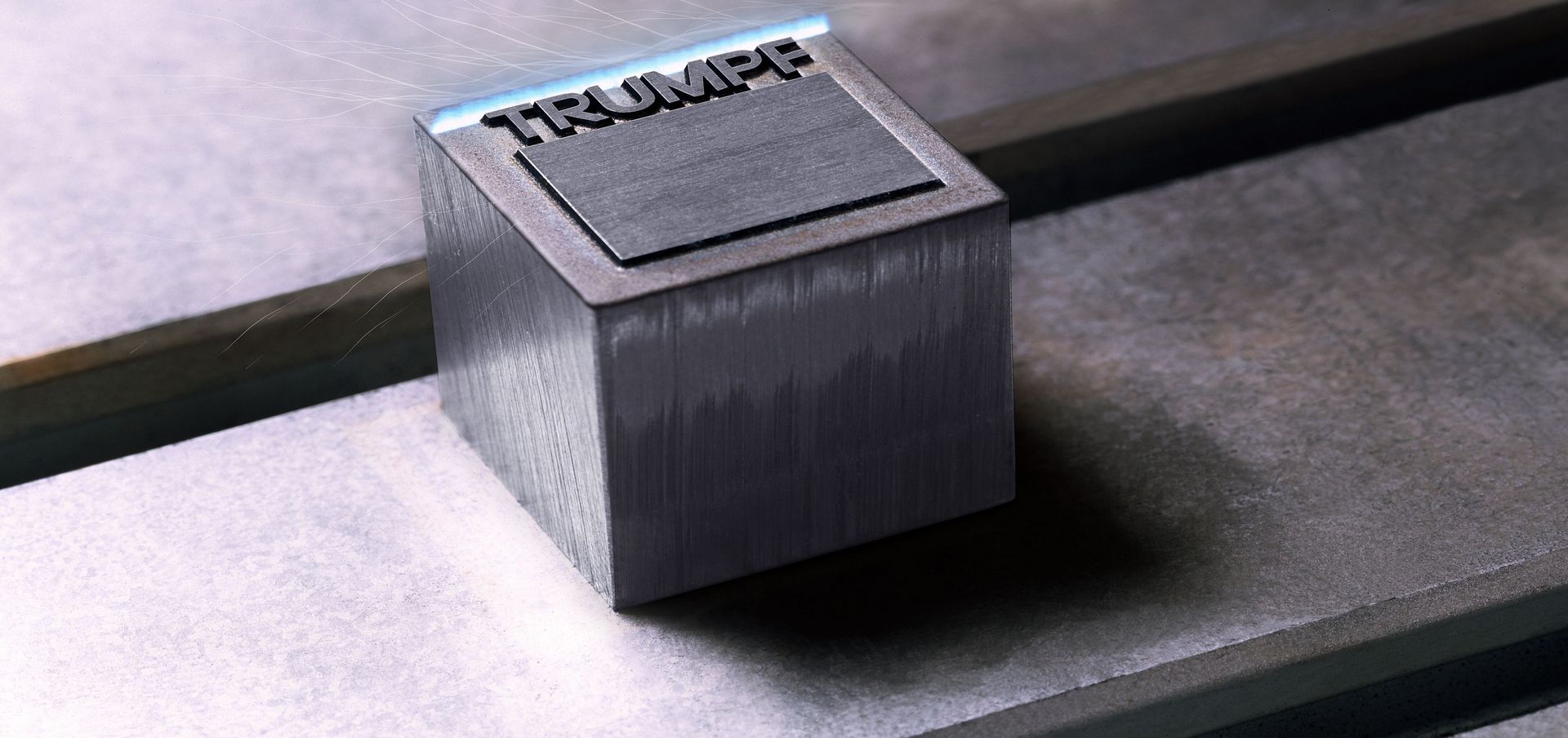
レーザーエングレービングとは?
レーザーエングレービングでは、レーザ光線が材料を除去することで、様々な表面構造を持つくぼみ、すなわちレーザー刻印が生み出されます。レーザーエングレービングは多種多様な材料に利用可能です。例えば金属のレーザーエングレービングでは、黒くて粗い構造と白くて滑らかな構造が形成されます。
レーザーエングレービングは自動車業界や電気工学で頻繁に使用されています。また、ラピッドプロトタイピングとラピッドツーリングでも、レーザーエングレービングによるマーキングとディープエングレービングが頻繁に行われています。
レーザーエングレービング工法のプロセス
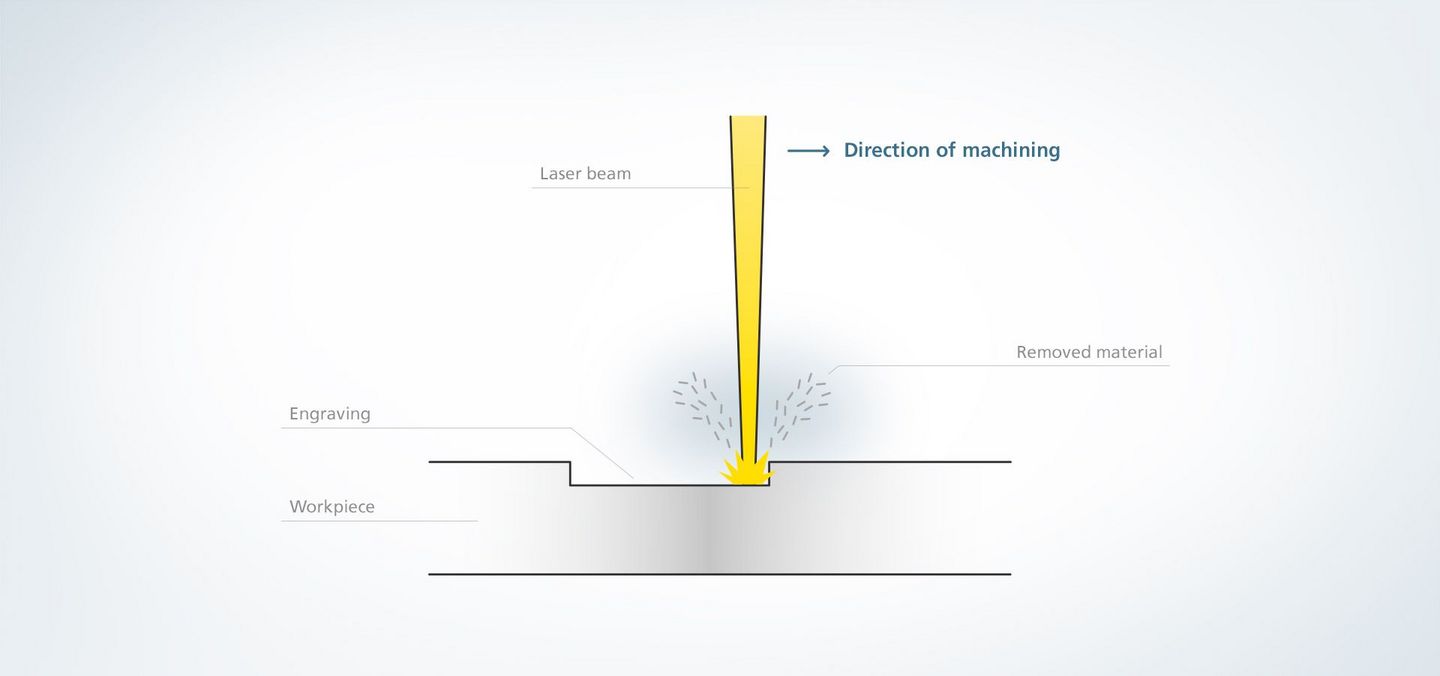
レーザーエングレービングでは、溶融と蒸発による除去を組み合わせてマーキングが施されます。レーザー光線の極めて高い照射強度により、加工中に材料が溶融して部分的に蒸発します。そして加工品にくぼみ、すなわちレーザー刻印が生み出されます。刻印の典型的な深さは10~50 μmです。材料の蒸発で生じた圧力により、溶融物が端に押し出され、冷却時に凝固して溶融バリになります。刻印はU字形で、その幅はレーザーが材料に深く入り込むほど狭くなりますが、その理由は、溶融物を完全に押し出すことができなくなるためです。レーザースポットが小さいため入熱は局所的であり、超短パルスであるため入熱時間もごくわずかに制限されます。
こちらがレーザーエングレービング用に最も頻繁に使用されている手法です
レーザーエングレービングを選ぶ主な理由
非接触式の精密なツールであるレーザーは、材料のアブレーションとエングレービングに多くの利点をもたらします。パルス周波数とパルス持続時間が柔軟に選択可能であるため、どのようなレーザー刻印であっても材質と希望の品質に合わせて完全にカスタマイズして設定することができます。
アニーリングマーキングと比較すると、レーザーエングレービングでは材料への侵入深さが深めであるにもかかわらず、繰り返し率が高くサイクルタイムが短いため、プロセスの所要時間が短縮されます。
レーザーエングレービングでは材料にくぼみが発生するため、マーキングは外的要因に対して極めて高い耐性を有します。
入熱が局所的であるため、熱に弱いセンサーや電子チップなどにもマーキングを施すことができます。
レーザー出力の的確な制御が可能であるため、何度行っても常に同じマーキング結果が得られます。
充実した内容のハンドブック「コンパクト版レーザーマーキング」には、プロセス、レーザー装置と実用的なマーキングのガイドラインに関する技術的な背景が記載されています。こちらからダウンロード可能です!
