1. Extreme seal welding
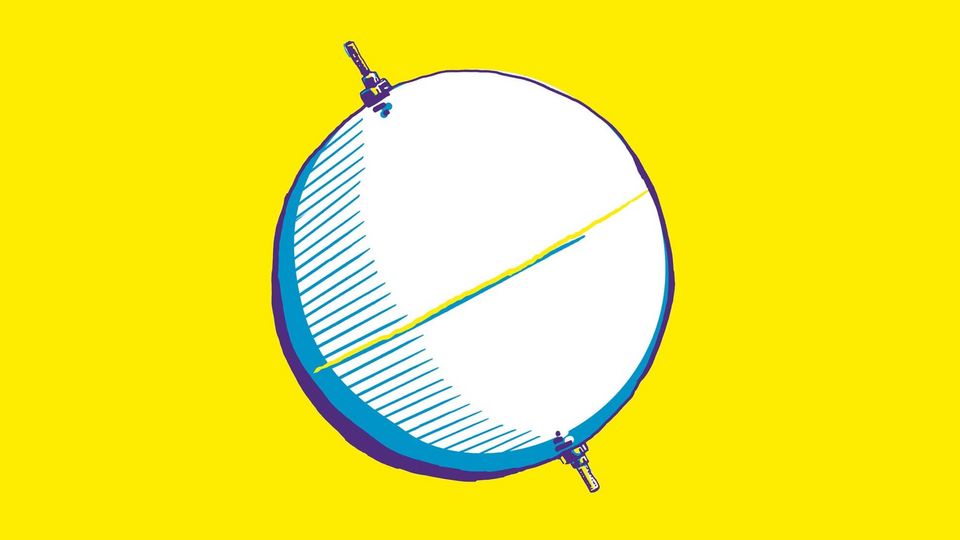
Seal-welded spherical tank
Two products brought the breakthrough for high-precision laser seal welding: first pacemakers and then electric car batteries. And now the space industry is exploiting this know-how to join materials such as stainless steel, aluminum, titanium, and superalloys like Inconel. The chief benefits are high process speed, which can reach as much as several meters per minute, and neat, smooth seams, achieved thanks to the use of sensors to control the application of energy. Laser seal welding is rapidly becoming standard practice in one area of particular importance: rocket tanks. If service engineers discover even the tiniest of leaks, the launch has to be aborted. If it remains undetected, disaster will strike as soon as the engines are ignited. Which is why aerospace companies prefer to play it safe and use lasers.
2. Hybrid joints
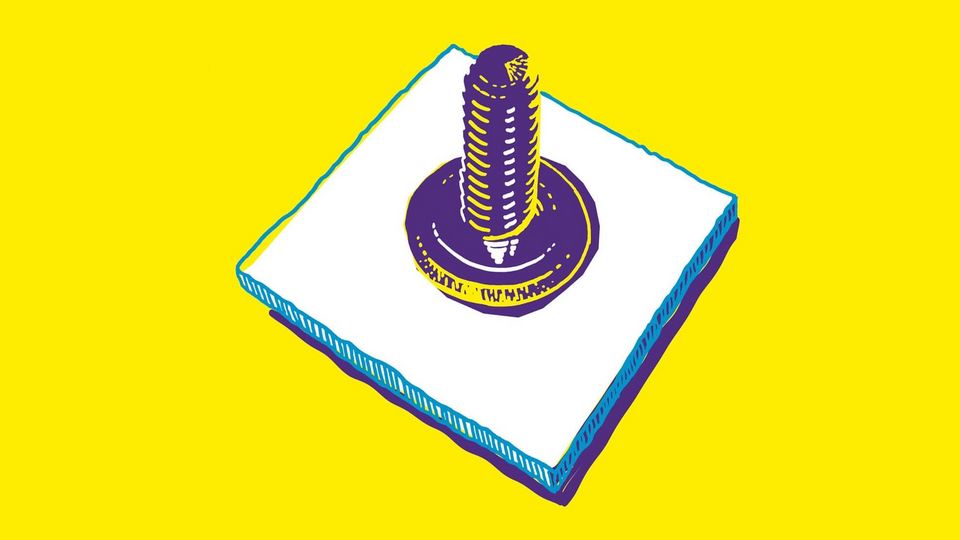
Direct joining of plastic and metal
Ultrashort pulse lasers apply their energy so precisely that they can be used to join different materials with a gastight, fracture-proof weld. For example, glass and metal. Such combinations are especially attractive for the manufacture of optical components for satellites and perhaps even for the windows of space stations. The prime virtue of this type of laser weld is that it joins the two materials directly. In other words, there is no need for laborious screw joints or temperature-sensitive adhesives–both of which also add weight. NASA has already tested an ultrashort pulse laser to weld glass and Invar, a special alloy, and is now planning to make use of this technique. In many cases, the only way to use glass in space is to directly join glass to other materials or to use a glass-glass joint. Increasingly, conventional screw joints are also being replaced by directly welding, with a short-pulse laser, metals to carbon fiber-reinforced.
3. 3D-printed components
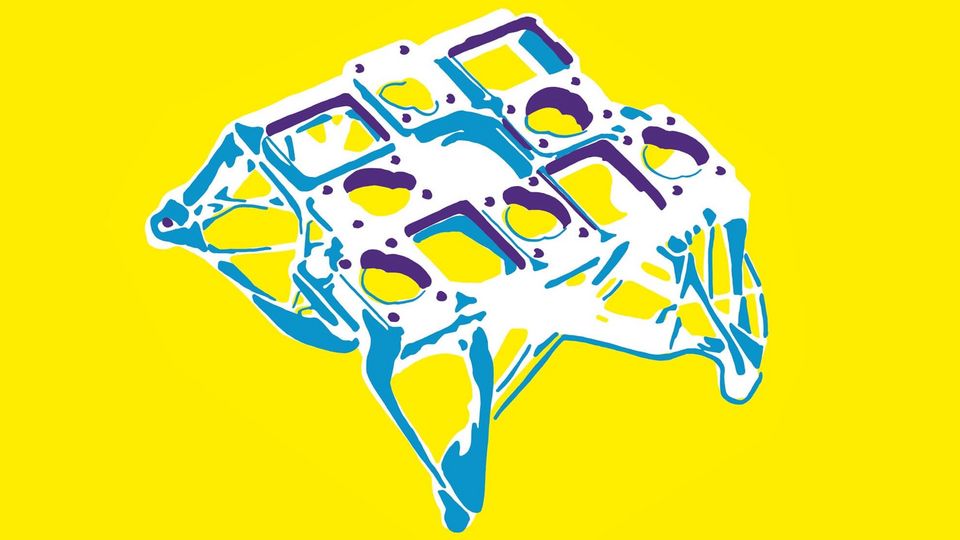
Camera mount for satellites
Every kilo saved makes space flight cheaper. This applies to rockets, because a lower weight means they can carry a greater payload; and it also applies to the payload itself, the cost of which falls with decreasing weight. This was what first drove the introduction of additive manufacturing for structural components such as camera mounts, which use as little material as possible and are constructed along purely functional lines. It is now clear that this approach has made components not only lighter but also more robust, because it enables better designs. What’s more, additive manufacturing with temperature-resistant superalloysuch as Inconel turns out to be substantially cheaper than conventional mechanical processes such as turning. When it comes to space, 3D printing is almost always the best option.
4. Satellite communications
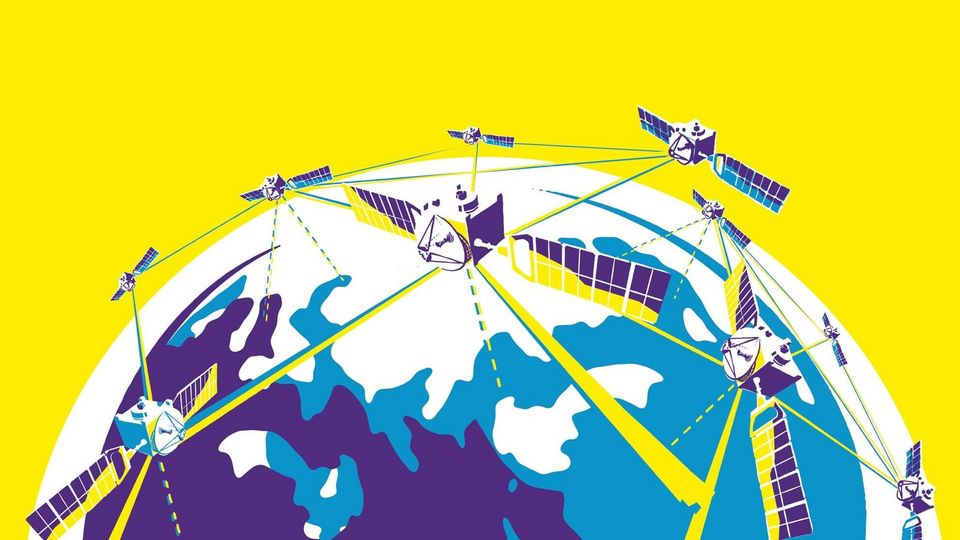
Data transfer via laser
In the future, laser signals will be used to transmit data in space. LEO satellites race around the globe at around 7.8 kilometers per second–much too fast for stable data transmission. That’s why contact to a network of several LEO satellites is always required, as one of them is always just flying out of range. In the future, LEO satellites will use laser beams to exchange data while in orbit, across thousands of kilometers. And data transfer from satellite to ground will also switch to this technology, as lasers transmit at a rate of up to 100 times faster than radio waves. With data transmission increasing rapidly on account of streaming, AI cloud computing, the Internet of Things, and a host of other data services, that has to be good news. What’s more, physical constraints prevent laser communications from being intercepted. Any attempt at espionage would be detected immediately. High-tech military satellites already employ satellite-to-satellite and satellite-toground laser communications. Experts forecast that the technology will also become established in commercial networks in ten years from now.
Additive manufacturing for engines and thrusters- with copper!
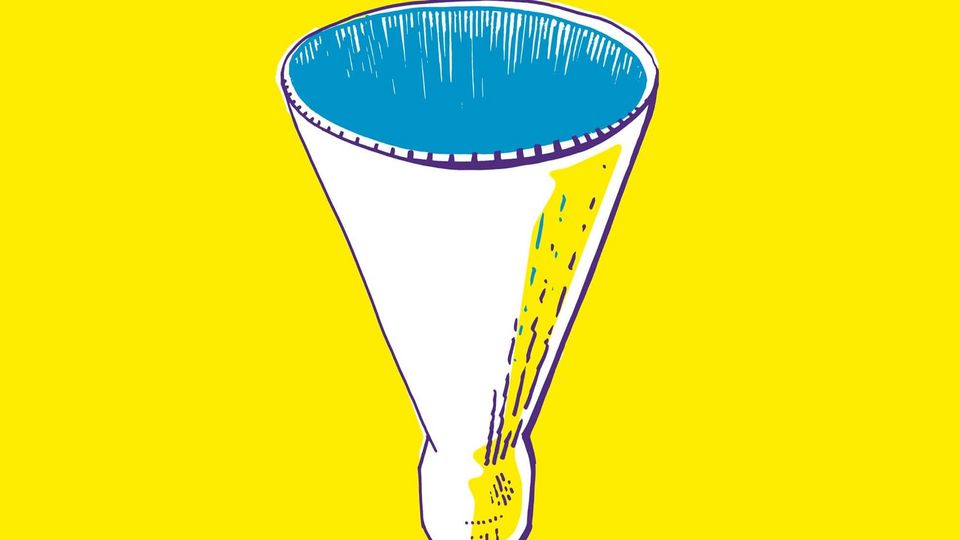
Bimetal rocket nozzle
To function properly, rockets engines and thrusters–small propulsion devices to control orientation, acceleration, and deceleration of probes and satellites–feature a system of fine cooling channels for the propellant. For mini-thrusters, additive manufacturing is the only option on account of the minimal wall thickness; and for larger thrusters, it represents the cheapest method. Laser metal deposition (LMD) is also suitable for larger components with internal channels, such as engine nozzles. Equally, LMD can be used to fabricate bimetal structures and deposits each metal according to the desired functionality of the finished part. In the case of the nozzle, this means copper on the inside for maximal heat flow and a tough layer of Inconel on the outside for strength.