One advantage of black marking is the "viewing angle consistency". The very high, even contrast from all viewing angles is the result of periodic nanostructures which reflect the light in a very scattered manner, as well as absorb it. This represents a quality attribute, especially in the watch and automotive industry, where many visible parts are used.
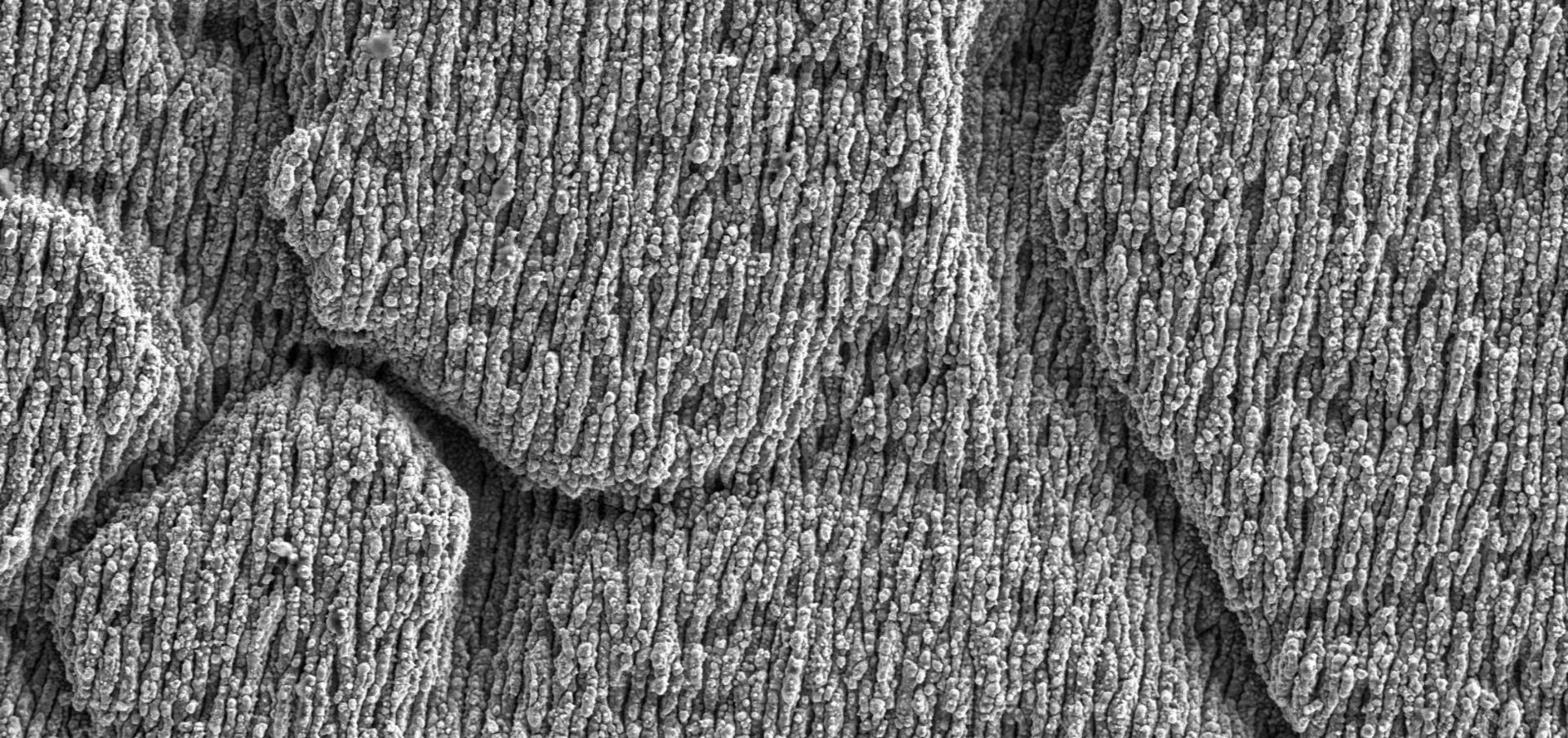
Black marking – permanent, deep-black and corrosion-resistant markings
Black marking is a procedure in laser processing which causes extremely dark, high-contrast markings on a surface without material ablation. Extremely short laser pulses cause structures on the surface at the nanometer level. The microstructured surface ensures that light scattering is reduced, and creates a marking with constant depth and a consistent black colour. When the laser pulses used for this marking are ultrashort, the colour changes also remain corrosion-resistant within certain parameter ranges. The reason for this is that the use of ultrashort pulse lasers means that the heat-affected zone is extremely small, meaning that enough free chrome remains on the surface that a self-healing oxide film can form.
An overview of your advantages
Curious about the advantages that black marking could bring to your marking task?
Our experts would be pleased to advise you.
White paper: corrosion-resistant black marking
Read our white paper on black marking and its applications in medical technology. Click here for the white paper!
Process description
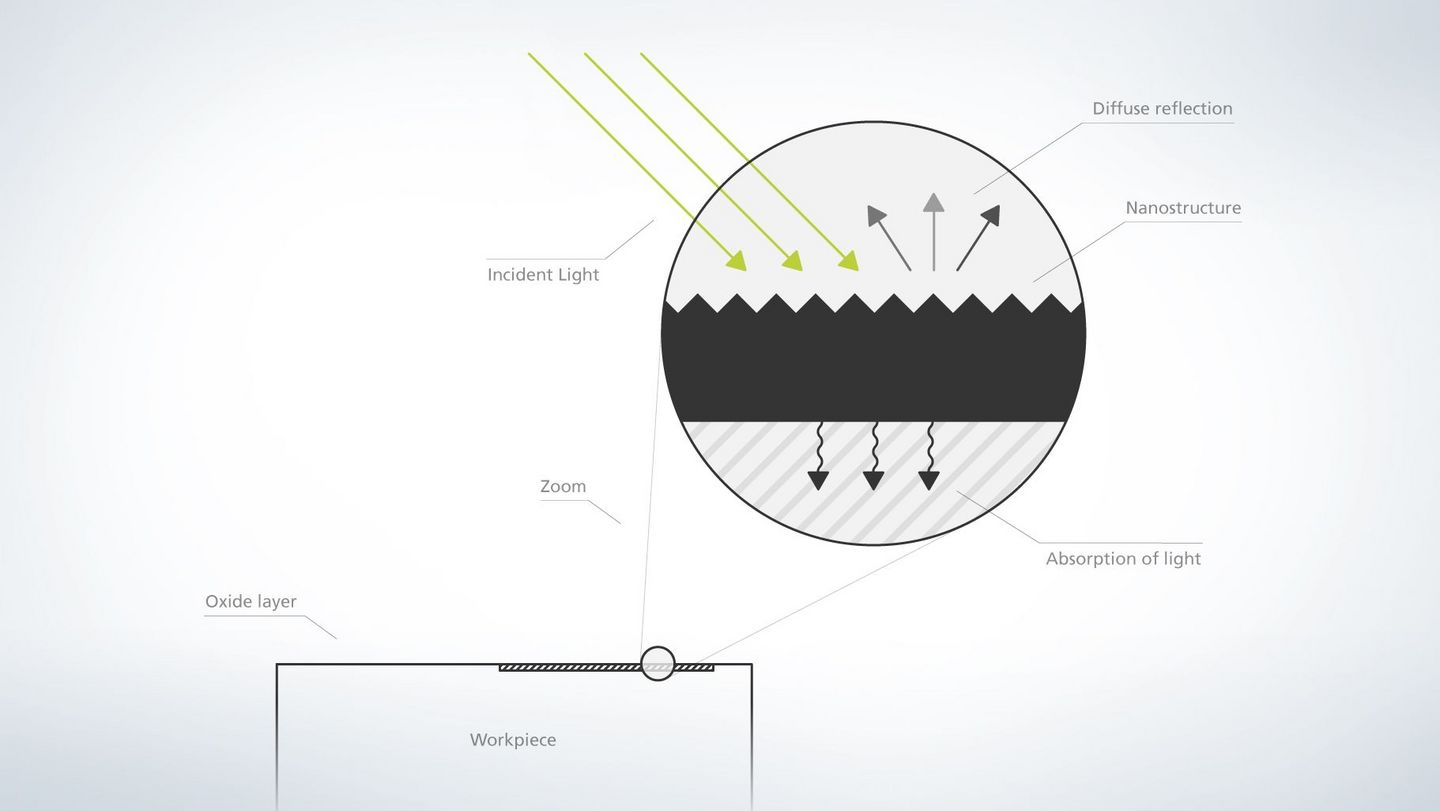
- Surface structure: Ultrashort pulse lasers with a pulse duration in the range of pico or femtoseconds provide the basis for corrosion-resistant black marking. It becomes possible to process materials with virtually no thermal or mechanical impact. This is because the laser pulse, and therefore the duration of the energy input, is so short that temperature transport to neighboring atoms does not even occur. This prevents thermal stress cracks which can occur in conventional annealing when the parameters are not considered. This is why it is referred to as "cold processing". The laser structures the material at the nanometer level.
- Oxide film: In addition to surface structuring, a chromium oxide film plays the second central role in corrosion-resistant black marking. The low exposure to heat in comparison to annealing with short-pulse lasers allows for a sufficient amount of chrome to remain on the surface, which promotes the self-healing process of the passive film. This creates more corrosion-resistant films with chromite (Fe2+Cr2O4) and magnetite (Fe3O4), as well as films consisting of a mixed phase: FeFe2-xCrxO4 (iron-chrome-spinel).
- Passivation: Marking is followed by the cleaning of the medical products. The legibility and durability of laser marking can be affected by prolonged exposure times, aggressive cleaning agents or high temperatures. This is why a targeted passivation procedure is often opted for when it comes to refinishing. In this process, an acid bath consisting of saltpetre or citric acid removes highly reactive elements (e.g. free iron ions) from the surface, and supports the clean, fast formation of a new chrome oxide film for even better corrosion resistance. At the same time, the surface is also cleaned and sulphid es removed during this process.
Find your perfect marking laser now
Use the TruMark product finder to discover which marking laser is best suited to your application!
Applications examples for black marking
Black marking with TruMicro Mark
In this video, you can see how the TruMicro Mark uses black marking to apply a jet-black, traceable and corrosion-resistant UDI code (Unique Device Identification) to the component.
White paper
We have compiled a selection of white papers on topics that may be of interest to you
Curious about the advantages that black marking could bring to your marking task?
Our experts would be pleased to advise you.