That depends, the decisive factor at the end of the day is the part costs. And you can often lower these significantly with automated welding. In addition, entry-level solutions and financing models are available which we can adapt to your situation along with you. You can either buy the system, hire purchase, lease or pay in full or in affordable payments. You will be laying a solid foundation for the future of your company.
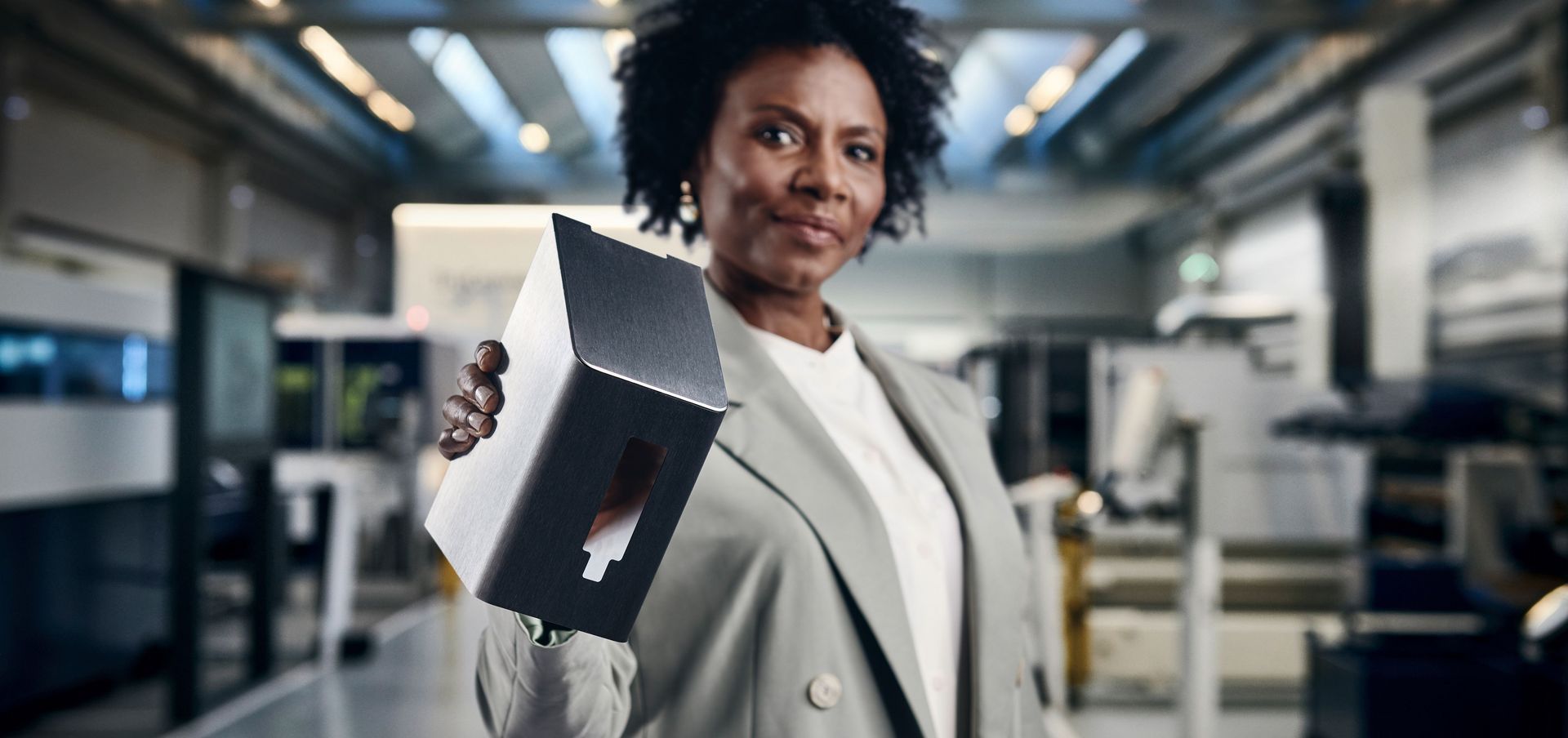
How to cap your costs with welding systems
Smaller lot sizes, rising cost pressure: the competition is becoming increasingly tougher for sheet metal processors. At the moment, the welding process is the greatest cost driver. Use this lever to make savings. Bring the efficiency of a fully synchronized production into your company with an automated welding system – putting you one step ahead for future quotes.
Automated welding pays off for you
Numbers don't lie. We therefore show you a financial comparison of manual TIG welding and laser welding. The workpiece: a hood made of mild steel which has to satisfy high visual requirements.
The result: when joining with laser welding, you can reduce the time required by up to 90% and costs per part by 65%. If you utilize up to 50% of your system in a shift with these types of components, it pays off in around two years.
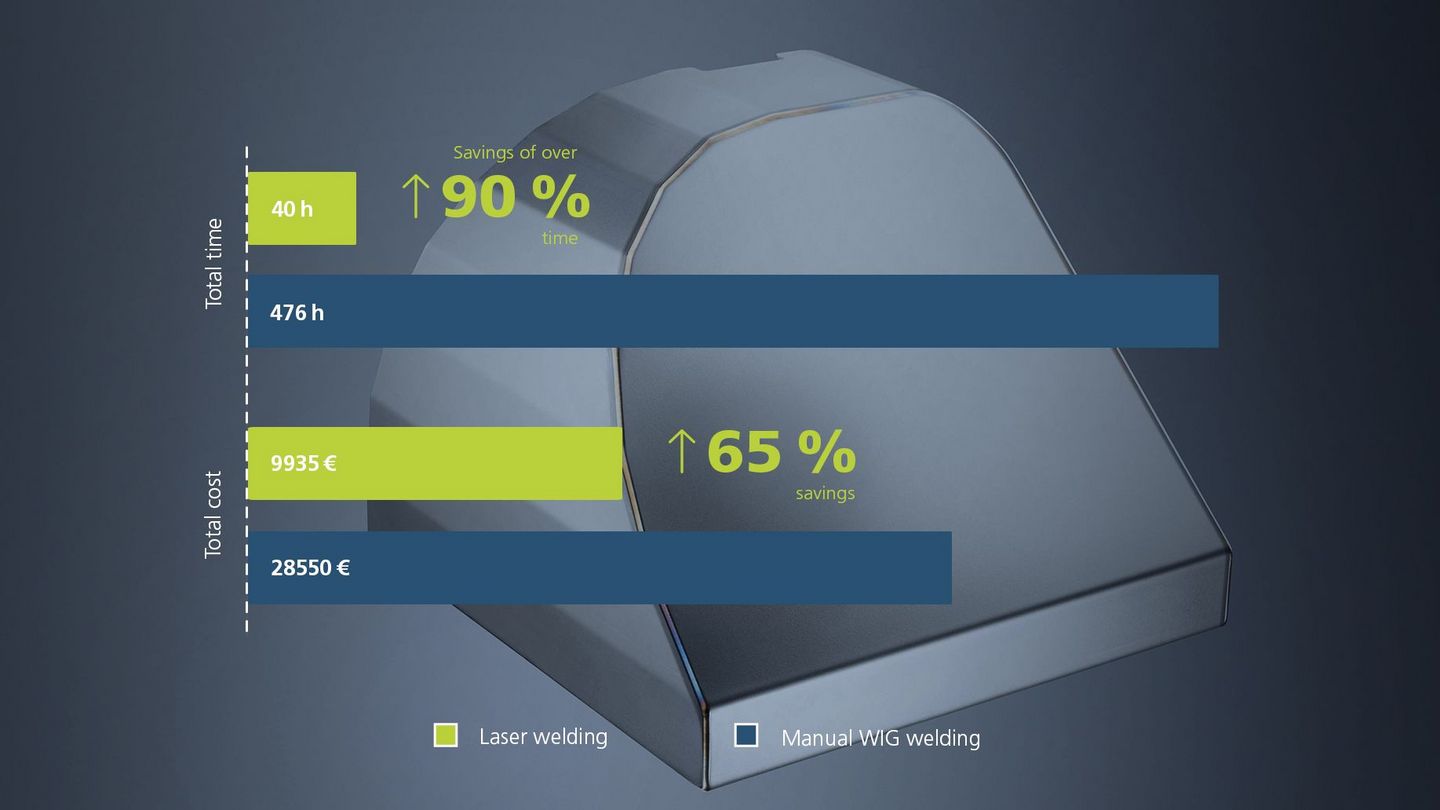
This calculation is based on average values typical for Germany and a quantity of 500 hoods that are produced in 10 units of 50 pieces each. In the case of TIG manual welding, the welding time per part is approx. 45 minutes; when using automated laser welding, it is only approx. 2 minutes. Reworking is also eliminated when laser welding this hood. In the case of a conventional welding process, this adds another 10 minutes to each part. This gain in time per part more than compensates for time spent programming the order, the costs for the fixture and the setup time per lot, which are comparatively higher in the case of laser welding.
This is what users are saying
We understand the challenges you face
Automated welding pays off
Automated welding pays off from a lot size of 1. You program and weld a simple weld seam in less than a minute with the TruArc Weld 1000. This means that automated arc welding saves time by 21 % even for this single console.

Consultation
Catapult your welding production into a new league: the welding experts from TRUMPF partner with you if you have any questions.